Kiekkojen kuutiointitekniikka, joka on kriittinen vaihe puolijohteiden valmistusprosessissa, liittyy suoraan sirun suorituskykyyn, saantoon ja tuotantokustannuksiin.
#01 Vohvelikuorintaprosessin tausta ja merkitys
1.1 Kiekkojen kuutioinnin määritelmä
Kiekkojen paloittelu (tunnetaan myös nimellä uurtaminen) on olennainen vaihe puolijohdevalmistuksessa, jonka tarkoituksena on jakaa käsitellyt kiekot useiksi yksittäisiksi siruiksi. Nämä sirut sisältävät tyypillisesti täydellisen piiritoiminnallisuuden ja ovat keskeisiä komponentteja, joita lopulta käytetään elektronisten laitteiden tuotannossa. Sirusuunnittelun monimutkaistuessa ja mittojen pienentyessä kiekkojen paloitteluteknologian tarkkuus- ja tehokkuusvaatimukset tiukentuvat entisestään.
Käytännössä kiekkojen paloittelussa käytetään tyypillisesti tarkkuustyökaluja, kuten timanttiteriä, sen varmistamiseksi, että jokainen siru pysyy ehjänä ja täysin toimivana. Keskeisiä vaiheita ovat valmistelu ennen leikkausta, tarkka ohjaus leikkausprosessin aikana ja laadunvalvonta leikkauksen jälkeen.
Ennen leikkaamista kiekko on merkittävä ja sijoitettava tarkkojen leikkausreittien varmistamiseksi. Leikkauksen aikana parametreja, kuten työkalun painetta ja nopeutta, on valvottava tarkasti kiekon vaurioitumisen estämiseksi. Leikkauksen jälkeen suoritetaan kattavat laatutarkastukset sen varmistamiseksi, että jokainen siru täyttää suorituskykystandardit.
Kiekkojen paloittelutekniikan perusperiaatteet kattavat paitsi leikkauslaitteiden valinnan ja prosessiparametrien asettamisen, myös materiaalien mekaanisten ominaisuuksien ja piirteiden vaikutuksen leikkauksen laatuun. Esimerkiksi matalan k-arvon dielektriset piikiekot ovat heikompien mekaanisten ominaisuuksiensa vuoksi erittäin alttiita jännityskeskittymälle leikkauksen aikana, mikä johtaa lohkeamiseen ja halkeiluun. Matala-k-arvoisten materiaalien alhainen kovuus ja hauraus tekevät niistä alttiimpia rakenteellisille vaurioille mekaanisen voiman tai lämpörasituksen alaisena, erityisesti leikkauksen aikana. Työkalun ja kiekon pinnan välinen kosketus yhdistettynä korkeisiin lämpötiloihin voi entisestään pahentaa jännityskeskittymää.
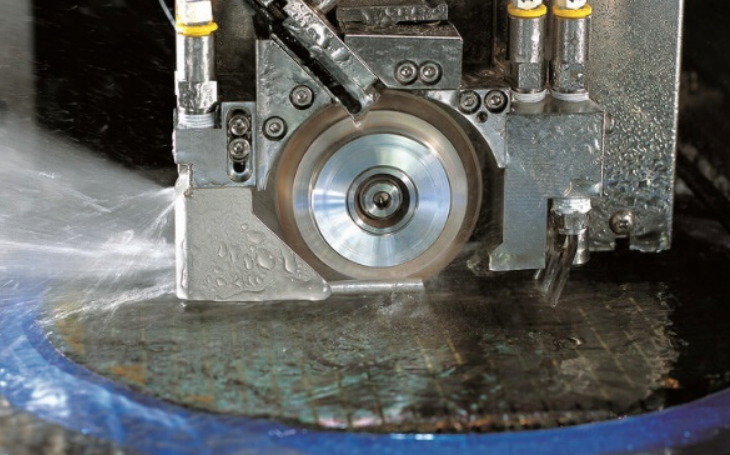
Materiaalitieteen edistyessä kiekkojen kuutiointitekniikka on laajentunut perinteisten piipohjaisten puolijohteiden ulkopuolelle kattamaan uusia materiaaleja, kuten galliumnitridiä (GaN). Nämä uudet materiaalit asettavat kovuuden ja rakenteellisten ominaisuuksiensa vuoksi uusia haasteita kuutiointiprosesseille, mikä vaatii leikkaustyökalujen ja -tekniikoiden parantamista.
Puolijohdeteollisuuden kriittisenä prosessina kiekkojen paloittelua optimoidaan jatkuvasti vastauksena kehittyviin vaatimuksiin ja teknologiseen kehitykseen, mikä luo pohjan tulevaisuuden mikroelektroniikalle ja integroitujen piirien teknologioille.
Kiekkojen kuutiointiteknologian parannukset ulottuvat apumateriaalien ja työkalujen kehittämistä pidemmälle. Ne kattavat myös prosessien optimoinnin, laitteiden suorituskyvyn parantamisen ja kuutiointiparametrien tarkan hallinnan. Näiden edistysaskeleiden tavoitteena on varmistaa kiekkojen kuutiointiprosessin korkea tarkkuus, tehokkuus ja vakaus, mikä vastaa puolijohdeteollisuuden tarpeisiin pienemmille mitoille, paremmalle integroinnille ja monimutkaisemmille sirurakenteille.
parannusalue | Erityistoimenpiteet | Vaikutukset |
Prosessien optimointi | - Parantaa alkuvaiheen valmisteluja, kuten tarkempaa kiekkojen asemointia ja reitin suunnittelua. | - Vähentää leikkausvirheitä ja parantaa vakautta. |
- Minimoi leikkausvirheet ja paranna vakautta. | - Ota käyttöön reaaliaikaiset valvonta- ja takaisinkytkentämekanismit työkalun paineen, nopeuden ja lämpötilan säätämiseksi. | |
- Alhaisemmat kiekkojen rikkoutumisnopeudet ja paremmat sirun laadut. | ||
Laitteiden suorituskyvyn parantaminen | - Käytä erittäin tarkkoja mekaanisia järjestelmiä ja edistynyttä automaatio-ohjausteknologiaa. | - Paranna leikkaustarkkuutta ja vähennä materiaalihukkaa. |
- Esittelee laserleikkausteknologian, joka soveltuu erittäin kovien materiaalien kiekoille. | - Paranna tuotannon tehokkuutta ja vähennä manuaalisia virheitä. | |
- Lisää laitteiden automaatiota automaattista valvontaa ja säätöjä varten. | ||
Tarkka parametrien hallinta | - Hienosäädä parametreja, kuten leikkaussyvyyttä, nopeutta, työkalutyyppiä ja jäähdytysmenetelmiä. | - Varmista sirun eheys ja sähköinen suorituskyky. |
- Mukauta parametreja kiekkomateriaalin, paksuuden ja rakenteen perusteella. | - Paranna saantoa, vähennä materiaalihävikkiä ja alenna tuotantokustannuksia. | |
Strateginen merkitys | - Tutki jatkuvasti uusia teknologisia kehityspolkuja, optimoi prosesseja ja paranna laitteiden ominaisuuksia markkinoiden vaatimusten täyttämiseksi. | - Parantaa sirujen valmistuksen tuottoa ja suorituskykyä tukemalla uusien materiaalien ja edistyneiden sirusuunnittelujen kehittämistä. |
1.2 Kiekkojen kuutioinnin merkitys
Kiekkojen paloittelulla on ratkaiseva rooli puolijohteiden valmistusprosessissa, ja se vaikuttaa suoraan seuraaviin vaiheisiin sekä lopputuotteen laatuun ja suorituskykyyn. Sen merkitys voidaan eritellä seuraavasti:
Ensinnäkin kuutioinnin tarkkuus ja johdonmukaisuus ovat avainasemassa sirun saannon ja luotettavuuden varmistamisessa. Valmistuksen aikana kiekot käyvät läpi useita käsittelyvaiheita muodostaen lukuisia monimutkaisia piirirakenteita, jotka on jaettava tarkasti yksittäisiksi siruiksi (siruiksi). Jos kuutiointiprosessin aikana on merkittäviä kohdistus- tai leikkausvirheitä, piirit voivat vaurioitua, mikä vaikuttaa sirun toimivuuteen ja luotettavuuteen. Siksi erittäin tarkka kuutiointitekniikka ei ainoastaan varmista jokaisen sirun eheyttä, vaan myös estää sisäisten piirien vaurioitumisen, mikä parantaa kokonaistuottoastetta.
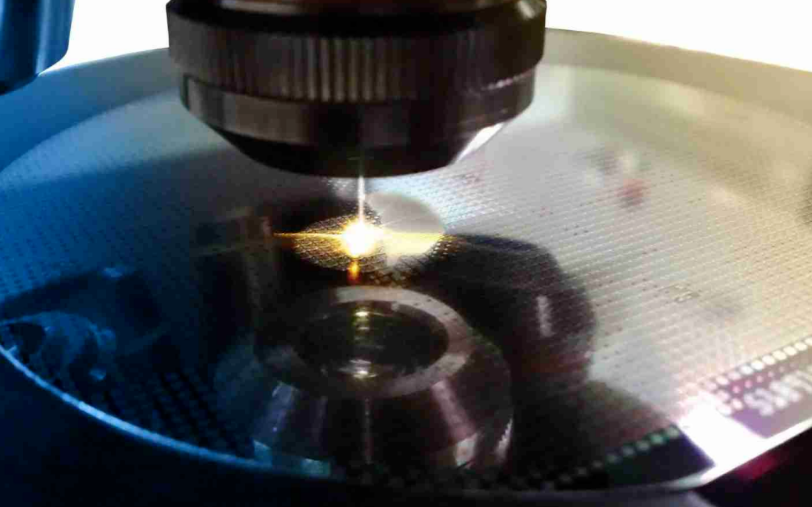
Toiseksi, kiekkojen kuutioinnilla on merkittävä vaikutus tuotantotehokkuuteen ja kustannusten hallintaan. Valmistusprosessin ratkaisevana vaiheena sen tehokkuus vaikuttaa suoraan seuraavien vaiheiden etenemiseen. Optimoimalla kuutiointiprosessia, lisäämällä automaatiotasoa ja parantamalla leikkausnopeuksia voidaan parantaa huomattavasti kokonaistuotannon tehokkuutta.
Toisaalta materiaalihävikki kuutioinnin aikana on kriittinen tekijä kustannusten hallinnassa. Edistyneiden kuutiointitekniikoiden hyödyntäminen ei ainoastaan vähennä tarpeetonta materiaalihävikkiä leikkausprosessin aikana, vaan myös lisää kiekkojen käyttöastetta ja siten alentaa tuotantokustannuksia.
Puolijohdetekniikan kehittyessä kiekkojen halkaisijat kasvavat jatkuvasti ja piirien tiheydet kasvavat vastaavasti, mikä asettaa suurempia vaatimuksia kuutiointitekniikalle. Suuremmat kiekot vaativat leikkausreittien tarkempaa hallintaa, erityisesti tiheästi rakennetuilla piirialueilla, joissa pienetkin poikkeamat voivat tehdä useista siruista vikoja. Lisäksi suuremmissa kiekoissa on enemmän leikkauslinjoja ja monimutkaisempia prosessivaiheita, mikä edellyttää kuutiointitekniikoiden tarkkuuden, yhdenmukaisuuden ja tehokkuuden parantamista näiden haasteiden ratkaisemiseksi.
1.3 Kiekkojen kuutiointiprosessi
Kiekkojen kuutiointiprosessi kattaa kaikki vaiheet valmisteluvaiheesta lopulliseen laaduntarkastukseen, ja jokainen vaihe on kriittinen kuutioitujen sirujen laadun ja suorituskyvyn varmistamiseksi. Alla on yksityiskohtainen selitys jokaisesta vaiheesta.
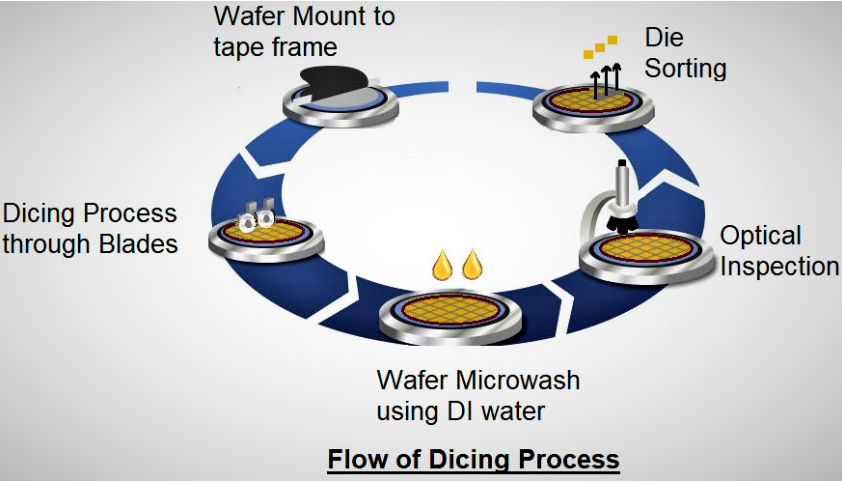
Vaihe | Yksityiskohtainen kuvaus |
Valmisteluvaihe | -Kiekkojen puhdistusKäytä erittäin puhdasta vettä ja erikoispuhdistusaineita yhdistettynä ultraääni- tai mekaaniseen hankaukseen epäpuhtauksien, hiukkasten ja kontaminanttien poistamiseksi ja varmista puhtaan pinnan varmistaminen. -Tarkka paikannusKäytä tarkkuuslaitteita varmistaaksesi, että kiekko jaetaan tarkasti suunniteltuja leikkausreittejä pitkin. -Kiekkojen kiinnitysKiinnitä kiekko teippikehykseen vakauden säilyttämiseksi leikkauksen aikana ja tärinän tai liikkeen aiheuttamien vaurioiden estämiseksi. |
Leikkausvaihe | -Terän kuutiointiKäytä fyysiseen leikkaamiseen nopeita pyöriviä timanttipäällysteisiä teriä, jotka sopivat piipohjaisille materiaaleille ja ovat kustannustehokkaita. -LaserkuutiointiKäytä suuritehoisia lasersäteitä kosketuksettomaan leikkaukseen, mikä on ihanteellista hauraille tai koville materiaaleille, kuten galliumnitridille, ja tarjoaa paremman tarkkuuden ja pienemmän materiaalihävikin. -Uudet teknologiatOtetaan käyttöön laser- ja plasmaleikkaustekniikat tehokkuuden ja tarkkuuden parantamiseksi entisestään ja minimoimalla lämpövaikutusalueet. |
Puhdistusvaihe | - Käytä deionisoitua vettä (DI-vettä) ja erikoispuhdistusaineita yhdessä ultraääni- tai suihkupuhdistuksen kanssa poistaaksesi leikkauksen aikana syntyvät roskat ja pölyn, estäen jäämien vaikuttamasta seuraaviin prosesseihin tai sirun sähköiseen suorituskykyyn. - Erittäin puhdas deionisoitu vesi estää uusien epäpuhtauksien pääsyn laitteeseen ja varmistaa puhtaan kiekkoympäristön. |
Tarkastusvaihe | -Optinen tarkastusKäytä optisia tunnistusjärjestelmiä yhdessä tekoälyalgoritmien kanssa vikojen nopeaan tunnistamiseen, varmistaen, ettei paloitetuissa siruissa ole halkeamia tai lohkeamia, parantaen tarkastustehokkuutta ja vähentäen inhimillisiä virheitä. -MittamittausVarmista, että sirun mitat vastaavat suunnitteluvaatimuksia. -Sähköinen suorituskykytestausVarmista, että kriittisten sirujen sähköinen suorituskyky täyttää standardit ja takaa luotettavuuden myöhemmissä sovelluksissa. |
Lajitteluvaihe | - Käytä robottikäsivarsia tai imukuppeja erotellaksesi kelvolliset sirut nauhakehyksestä ja lajitellaksesi ne automaattisesti suorituskyvyn perusteella, mikä varmistaa tuotannon tehokkuuden ja joustavuuden samalla parantaen tarkkuutta. |
Kiekkojen leikkausprosessiin kuuluu kiekkojen puhdistus, asemointi, leikkaus, puhdistus, tarkastus ja lajittelu, ja jokainen vaihe on kriittinen. Automaation, laserleikkauksen ja tekoälytarkastustekniikoiden kehityksen myötä nykyaikaiset kiekkojen leikkausjärjestelmät voivat saavuttaa suuremman tarkkuuden, nopeuden ja pienemmän materiaalihävikin. Tulevaisuudessa uudet leikkaustekniikat, kuten laser ja plasma, korvaavat vähitellen perinteisen teräleikkauksen yhä monimutkaisempien sirurakenteiden tarpeiden täyttämiseksi, mikä vauhdittaa entisestään puolijohdevalmistusprosessien kehitystä.
Kiekkojen leikkaustekniikka ja sen periaatteet
Kuvassa on kolme yleistä kiekkojen leikkaustekniikkaa:Terän kuutiointi,LaserkuutiointijaPlasmakuutiointiAlla on yksityiskohtainen analyysi ja täydentävä selitys näistä kolmesta tekniikasta:
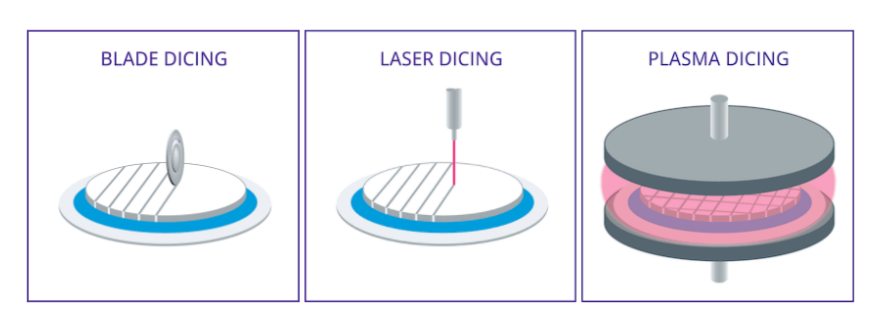
Puolijohdevalmistuksessa kiekkojen leikkaus on ratkaiseva vaihe, jossa on valittava sopiva leikkausmenetelmä kiekon paksuuden perusteella. Ensimmäinen vaihe on kiekon paksuuden määrittäminen. Jos kiekon paksuus ylittää 100 mikronia, leikkausmenetelmäksi voidaan valita terän paloittelu. Jos terän paloittelu ei sovellu, voidaan käyttää murtumaleikkausmenetelmää, joka sisältää sekä kaiverrusleikkauksen että terän paloittelun tekniikat.
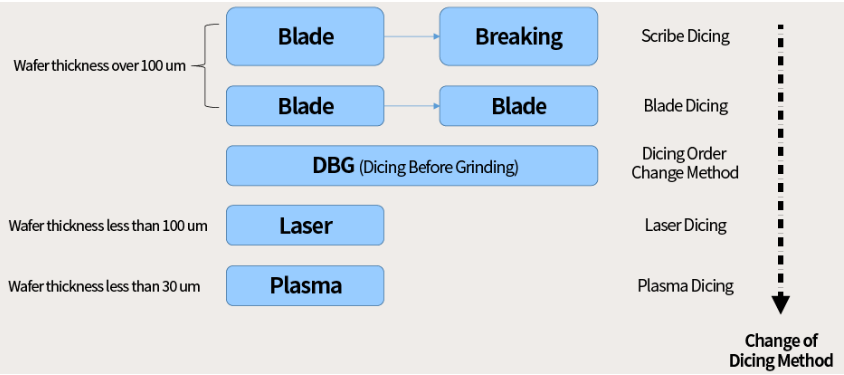
Kun kiekon paksuus on 30–100 mikronia, suositellaan DBG-menetelmää (Dice Before Grinding). Tässä tapauksessa parhaan tuloksen saavuttamiseksi voidaan valita viiltoleikkaus, terän pilkkominen tai leikkausjärjestyksen säätäminen tarpeen mukaan.
Alle 30 mikronin paksuisten erittäin ohuiden kiekkojen kohdalla laserleikkaus on ensisijainen menetelmä, koska se pystyy leikkaamaan ohuita kiekkoja tarkasti aiheuttamatta liiallisia vaurioita. Jos laserleikkaus ei pysty täyttämään tiettyjä vaatimuksia, vaihtoehtona voidaan käyttää plasmaleikkausta. Tämä vuokaavio tarjoaa selkeän päätöksentekopolun sen varmistamiseksi, että sopivin kiekkojen leikkaustekniikka valitaan eri paksuusolosuhteissa.
2.1 Mekaaninen leikkaustekniikka
Mekaaninen leikkaustekniikka on perinteinen menetelmä kiekkojen kuutioinnissa. Ydinperiaatteena on käyttää nopeaa pyörivää timanttihiomalaikkaa leikkaustyökaluna kiekon viipaloimiseksi. Keskeisiin laitteisiin kuuluu ilmalaakerikara, joka pyörittää timanttihiomalaikkaa suurilla nopeuksilla tarkan leikkauksen tai uran tekemiseksi ennalta määrättyä leikkausreittiä pitkin. Tätä tekniikkaa käytetään laajalti teollisuudessa sen alhaisten kustannusten, korkean hyötysuhteen ja laajan sovellettavuuden ansiosta.
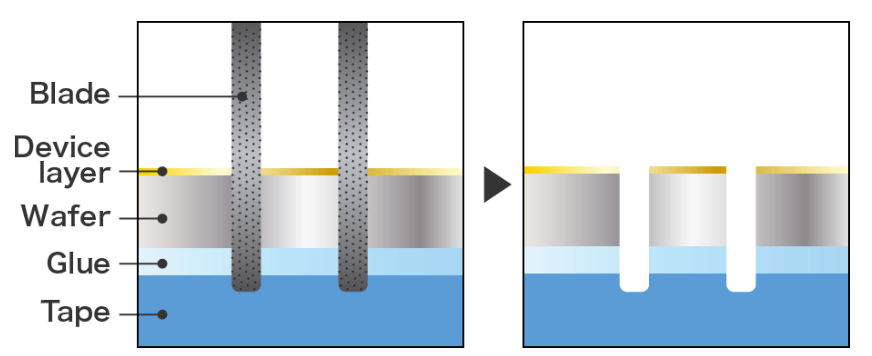
Edut
Timanttihiomalaikkojen korkea kovuus ja kulutuskestävyys mahdollistavat mekaanisen leikkausteknologian mukautumisen erilaisten kiekkomateriaalien leikkaustarpeisiin, olipa kyseessä sitten perinteiset piipohjaiset materiaalit tai uudemmat yhdistepuolijohteet. Sen käyttö on yksinkertaista ja tekniset vaatimukset suhteellisen alhaiset, mikä edistää sen suosiota massatuotannossa. Lisäksi mekaanisella leikkauksella on paremmin hallittavissa olevat kustannukset verrattuna muihin leikkausmenetelmiin, kuten laserleikkaukseen, mikä tekee siitä sopivan suurten volyymien tuotantotarpeisiin.
Rajoitukset
Lukuisista eduistaan huolimatta mekaanisella leikkaustekniikalla on myös rajoituksensa. Ensinnäkin työkalun ja kiekon välisen fyysisen kosketuksen vuoksi leikkaustarkkuus on suhteellisen rajallinen, mikä johtaa usein mittapoikkeamiin, jotka voivat vaikuttaa myöhemmän sirujen pakkauksen ja testauksen tarkkuuteen. Toiseksi mekaanisen leikkausprosessin aikana voi helposti esiintyä vikoja, kuten lohkeilua ja halkeamia, mikä ei ainoastaan vaikuta saantoon, vaan voi myös vaikuttaa negatiivisesti sirujen luotettavuuteen ja käyttöikään. Mekaanisen rasituksen aiheuttamat vauriot ovat erityisen haitallisia tiheiden sirujen valmistuksessa, erityisesti hauraita materiaaleja leikattaessa, missä nämä ongelmat ovat yleisempiä.
Teknologiset parannukset
Näiden rajoitusten voittamiseksi tutkijat optimoivat jatkuvasti mekaanista leikkausprosessia. Keskeisiin parannuksiin kuuluu hiomalaikkojen suunnittelun ja materiaalivalintojen parantaminen leikkaustarkkuuden ja kestävyyden parantamiseksi. Lisäksi leikkauslaitteiden rakenteellisen suunnittelun ja ohjausjärjestelmien optimointi on parantanut leikkausprosessin vakautta ja automaatiota entisestään. Nämä edistysaskeleet vähentävät ihmisen toiminnan aiheuttamia virheitä ja parantavat leikkausten tasaisuutta. Edistyneiden tarkastus- ja laadunvalvontatekniikoiden käyttöönotto leikkausprosessin aikana esiintyvien poikkeamien reaaliaikaiseen seurantaan on myös parantanut merkittävästi leikkauksen luotettavuutta ja saantoa.
Tuleva kehitys ja uudet teknologiat
Vaikka mekaanisella leikkaustekniikalla on edelleen merkittävä asema kiekkojen leikkauksessa, uudet leikkaustekniikat kehittyvät nopeasti puolijohdeprosessien kehittyessä. Esimerkiksi lämpölaserleikkaustekniikan soveltaminen tarjoaa uusia ratkaisuja mekaanisen leikkauksen tarkkuus- ja vikaongelmiin. Tämä kosketukseton leikkausmenetelmä vähentää kiekkoon kohdistuvaa fyysistä rasitusta, mikä vähentää merkittävästi lohkeamisen ja halkeilun esiintyvyyttä, erityisesti hauraampia materiaaleja leikattaessa. Tulevaisuudessa mekaanisen leikkausteknologian integrointi uusiin leikkaustekniikoihin tarjoaa puolijohdevalmistukseen enemmän vaihtoehtoja ja joustavuutta, mikä parantaa entisestään valmistuksen tehokkuutta ja sirun laatua.
Yhteenvetona voidaan todeta, että vaikka mekaanisella leikkaustekniikalla on tiettyjä haittoja, jatkuvat teknologiset parannukset ja sen integrointi uusiin leikkaustekniikoihin mahdollistavat sen, että sillä on edelleen tärkeä rooli puolijohdevalmistuksessa ja se säilyttää kilpailukykynsä tulevaisuuden prosesseissa.
2.2 Laserleikkaustekniikka
Laserleikkaustekniikka, uutena kiekkojen leikkausmenetelmänä, on vähitellen saavuttanut laajaa huomiota puolijohdeteollisuudessa suuren tarkkuutensa, mekaanisten kosketusvaurioiden puuttumisen ja nopeiden leikkausominaisuuksiensa ansiosta. Tämä tekniikka hyödyntää lasersäteen suurta energiatiheyttä ja fokusointikykyä pienen lämpövaikutusalueen luomiseksi kiekkomateriaalin pinnalle. Kun lasersäde kohdistetaan kiekkoon, syntyvä lämpöjännitys aiheuttaa materiaalin murtumisen määrätyssä kohdassa, jolloin saavutetaan tarkka leikkaus.
Laserleikkaustekniikan edut
• Korkea tarkkuusLasersäteen tarkka paikannuskyky mahdollistaa mikroni- tai jopa nanometritason leikkaustarkkuuden, mikä täyttää nykyaikaisen erittäin tarkan ja tiheän integroitujen piirien valmistuksen vaatimukset.
• Ei mekaanista kosketustaLaserleikkaus välttää fyysisen kosketuksen kiekkoon, mikä estää mekaanisessa leikkauksessa yleisiä ongelmia, kuten lohkeilua ja halkeilua, parantaen merkittävästi sirujen saantoa ja luotettavuutta.
• Nopea leikkausnopeusLaserleikkauksen suuri nopeus lisää tuotantotehokkuutta, mikä tekee siitä erityisen sopivan laajamittaisiin ja nopeisiin tuotantotilanteisiin.
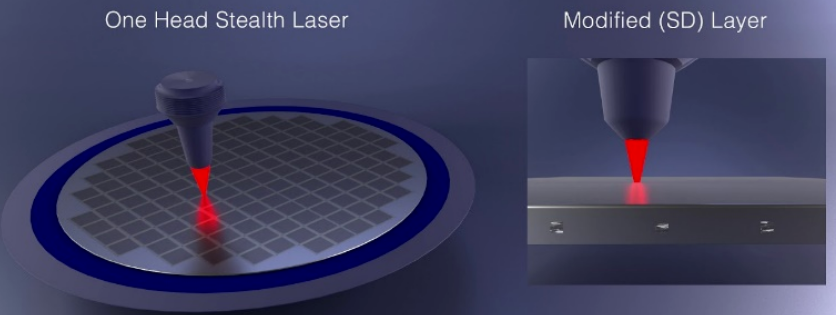
Kohdatut haasteet
• Korkeat laitekustannuksetLaserleikkauslaitteiden alkuinvestointi on korkea, mikä aiheuttaa taloudellista painetta erityisesti pienille ja keskisuurille tuotantoyrityksille.
• Monimutkainen prosessien hallintaLaserleikkaus vaatii useiden parametrien, kuten energiatiheyden, polttopisteen sijainnin ja leikkausnopeuden, tarkkaa hallintaa, mikä tekee prosessista monimutkaisen.
• Lämpötilan vaikutusalueen ongelmatVaikka laserleikkauksen kosketukseton luonne vähentää mekaanisia vaurioita, lämpövaikutusvyöhykkeen (HAZ) aiheuttama lämpöjännitys voi vaikuttaa negatiivisesti kiekkomateriaalin ominaisuuksiin. Prosessia on optimoitava edelleen tämän vaikutuksen minimoimiseksi.
Teknologisen parantamisen suunnat
Näiden haasteiden ratkaisemiseksi tutkijat keskittyvät laitekustannusten alentamiseen, leikkaustehokkuuden parantamiseen ja prosessivirran optimointiin.
• Tehokkaat laserit ja optiset järjestelmätKehittämällä tehokkaampia lasereita ja edistyneitä optisia järjestelmiä on mahdollista alentaa laitekustannuksia samalla kun leikkaustarkkuutta ja -nopeutta parannetaan.
• Prosessiparametrien optimointiLasereiden ja kiekkomateriaalien välistä vuorovaikutusta tutkitaan perusteellisesti, jotta voidaan parantaa prosesseja, jotka vähentävät lämpövaikutusaluetta ja siten parantavat leikkauslaatua.
• Älykkäät ohjausjärjestelmätÄlykkäiden ohjausteknologioiden kehittämisen tavoitteena on automatisoida ja optimoida laserleikkausprosessia, parantaen sen vakautta ja yhdenmukaisuutta.
Laserleikkaustekniikka on erityisen tehokasta erittäin ohuiden kiekkojen ja erittäin tarkkojen leikkausten tilanteissa. Kiekkojen koon kasvaessa ja piirien tiheyksien noustessa perinteisillä mekaanisilla leikkausmenetelmillä on vaikeuksia vastata nykyaikaisen puolijohdevalmistuksen tarkkuus- ja hyötysuhdevaatimuksiin. Ainutlaatuisten etujensa ansiosta laserleikkauksesta on tulossa ensisijainen ratkaisu näillä aloilla.
Vaikka laserleikkausteknologia kohtaa edelleen haasteita, kuten korkeita laitekustannuksia ja prosessien monimutkaisuutta, sen ainutlaatuiset edut suuressa tarkkuudessa ja kosketuksettomissa vaurioissa tekevät siitä tärkeän kehityssuunnan puolijohdevalmistuksessa. Laserteknologian ja älykkäiden ohjausjärjestelmien kehittyessä laserleikkauksen odotetaan parantavan edelleen kiekkojen leikkauksen tehokkuutta ja laatua, mikä edistää puolijohdeteollisuuden jatkuvaa kehitystä.
2.3 Plasmaleikkaustekniikka
Plasmaleikkaustekniikka, nousevana kiekkojen paloittelumenetelmänä, on saanut merkittävää huomiota viime vuosina. Tämä tekniikka käyttää korkeaenergisiä plasmasäteitä kiekkojen tarkkaan leikkaamiseen ohjaamalla plasmasäteen energiaa, nopeutta ja leikkausreittiä, jolloin saavutetaan optimaaliset leikkaustulokset.
Toimintaperiaate ja edut
Plasmaleikkausprosessi perustuu laitteen tuottamaan korkean lämpötilan ja energian omaavaan plasmasuihkuun. Tämä suihku voi lämmittää kiekkomateriaalin sulamis- tai höyrystymispisteeseen hyvin lyhyessä ajassa, mikä mahdollistaa nopean leikkauksen. Perinteiseen mekaaniseen tai laserleikkaukseen verrattuna plasmaleikkaus on nopeampaa ja tuottaa pienemmän lämpövaikutusalueen, mikä vähentää tehokkaasti halkeamien ja vaurioiden esiintymistä leikkauksen aikana.
Käytännön sovelluksissa plasmaleikkaustekniikka on erityisen taitava monimutkaisten muotoisten kiekkojen käsittelyssä. Sen korkeaenerginen, säädettävä plasmasäde voi helposti leikata epäsäännöllisen muotoisia kiekkoja suurella tarkkuudella. Siksi mikroelektroniikan valmistuksessa, erityisesti räätälöidyissä ja piensarjatuotannossa huippuluokan siruissa, tämä teknologia näyttää erittäin lupaavalta laajamittaiseen käyttöön.
Haasteet ja rajoitukset
Plasmaleikkaustekniikan monista eduista huolimatta sillä on myös joitakin haasteita.
• Monimutkainen prosessiPlasmaleikkausprosessi on monimutkainen ja vaatii erittäin tarkkoja laitteita ja kokeneita käyttäjiä sen varmistamiseksi,tarkkuus ja vakaus leikkauksessa.
• Ympäristönhallinta ja -turvallisuusPlasmasäteen korkean lämpötilan ja suuren energian luonne vaatii tiukkoja ympäristönvalvonta- ja turvallisuustoimenpiteitä, mikä lisää toteutuksen monimutkaisuutta ja kustannuksia.
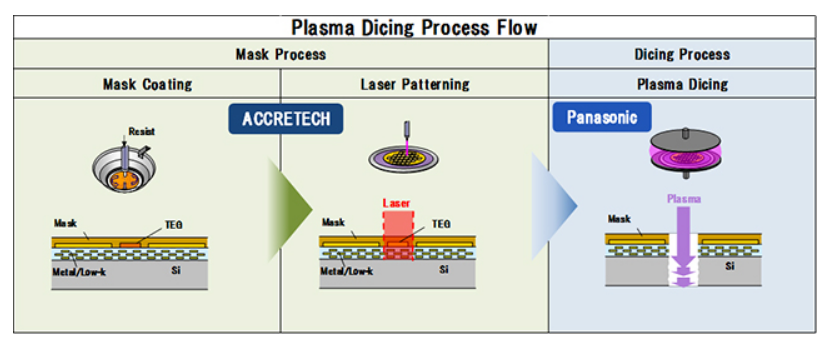
Tulevaisuuden kehityssuunnat
Teknologisen kehityksen myötä plasmaleikkaukseen liittyvien haasteiden odotetaan vähitellen voitettavan. Kehittämällä älykkäämpiä ja vakaampia leikkauslaitteita voidaan vähentää riippuvuutta manuaalisista toiminnoista ja siten parantaa tuotannon tehokkuutta. Samalla prosessiparametrien ja leikkausympäristön optimointi auttaa alentamaan turvallisuusriskejä ja käyttökustannuksia.
Puolijohdeteollisuudessa kiekkojen leikkaus- ja paloitteluteknologian innovaatiot ovat ratkaisevan tärkeitä alan kehityksen edistämiseksi. Plasmaleikkausteknologia, jolla on korkea tarkkuus, tehokkuus ja kyky käsitellä monimutkaisia kiekkomuotoja, on noussut merkittäväksi uudeksi toimijaksi tällä alalla. Vaikka joitakin haasteita on edelleen, näihin ongelmiin puututaan vähitellen jatkuvan teknologisen innovaation avulla, mikä tuo lisää mahdollisuuksia puolijohdevalmistukseen.
Plasmaleikkausteknologian sovellusmahdollisuudet ovat laajat, ja sen odotetaan olevan tulevaisuudessa entistä tärkeämmässä roolissa puolijohdevalmistuksessa. Jatkuvan teknologisen innovaation ja optimoinnin avulla plasmaleikkaus ei ainoastaan ratkaise nykyisiä haasteita, vaan siitä tulee myös voimakas puolijohdeteollisuuden kasvun ajuri.
2.4 Leikkauslaatu ja siihen vaikuttavat tekijät
Kiekkojen leikkauslaatu on ratkaisevan tärkeää myöhemmälle sirujen pakkaamiselle, testaukselle sekä lopputuotteen yleiselle suorituskyvylle ja luotettavuudelle. Yleisiä leikkauksen aikana ilmeneviä ongelmia ovat halkeamat, lohkeilu ja leikkauspoikkeamat. Näihin ongelmiin vaikuttavat useat tekijät yhdessä.
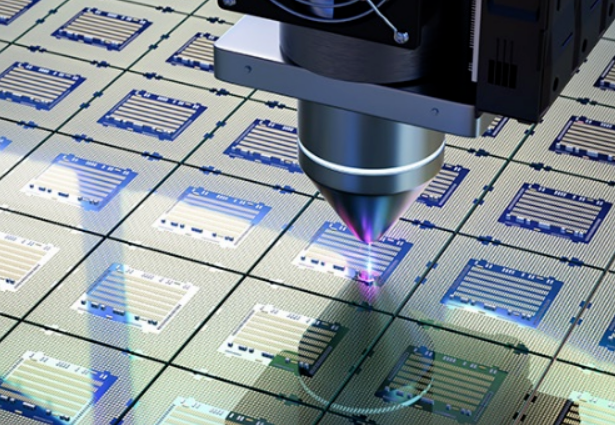
Kategoria | Sisältö | Vaikutus |
Prosessiparametrit | Leikkausnopeus, syöttönopeus ja leikkaussyvyys vaikuttavat suoraan leikkausprosessin vakauteen ja tarkkuuteen. Väärät asetukset voivat johtaa jännitysten keskittymiseen ja liialliseen lämpövaikutusalueeseen, mikä johtaa halkeamiin ja lohkeamiseen. Parametrien säätäminen asianmukaisesti kiekkomateriaalin, paksuuden ja leikkausvaatimusten perusteella on avain haluttujen leikkaustulosten saavuttamiseen. | Oikeat prosessiparametrit varmistavat tarkan leikkauksen ja vähentävät vikojen, kuten halkeamien ja lohkeilun, riskiä. |
Laitteet ja materiaalitekijät | -Terän laatuTerän materiaali, kovuus ja kulutuskestävyys vaikuttavat leikkausprosessin tasaisuuteen ja leikkauspinnan tasaisuuteen. Huonolaatuiset terät lisäävät kitkaa ja lämpöjännitystä, mikä voi johtaa halkeamiin tai lohkeiluun. Oikean terämateriaalin valinta on ratkaisevan tärkeää. -Jäähdytysnesteen suorituskykyJäähdytysnesteet auttavat alentamaan leikkauslämpötilaa, minimoimaan kitkaa ja poistamaan roskia. Tehoton jäähdytysneste voi johtaa korkeisiin lämpötiloihin ja roskien kertymiseen, mikä vaikuttaa leikkauslaatuun ja -tehokkuuteen. Tehokkaiden ja ympäristöystävällisten jäähdytysnesteiden valitseminen on erittäin tärkeää. | Terän laatu vaikuttaa leikkauksen tarkkuuteen ja tasaisuuteen. Tehoton jäähdytysneste voi johtaa heikkoon leikkauslaatuun ja -tehokkuuteen, mikä korostaa optimaalisen jäähdytysnesteen käytön tarvetta. |
Prosessinvalvonta ja laaduntarkastus | -ProsessinohjausKeskeisten leikkausparametrien reaaliaikainen valvonta ja säätö leikkausprosessin vakauden ja yhdenmukaisuuden varmistamiseksi. -LaaduntarkastusLeikkauksen jälkeiset ulkonäkötarkastukset, mittamittaukset ja sähköiset suorituskykytestit auttavat tunnistamaan ja korjaamaan laatuongelmat nopeasti, mikä parantaa leikkaustarkkuutta ja -tasaisuutta. | Asianmukainen prosessinohjaus ja laaduntarkastus auttavat varmistamaan tasaiset ja korkealaatuiset leikkaustulokset ja mahdollisten ongelmien varhaisen havaitsemisen. |

Leikkauslaadun parantaminen
Leikkauslaadun parantaminen vaatii kokonaisvaltaista lähestymistapaa, jossa otetaan huomioon prosessiparametrit, laitteiden ja materiaalien valinta, prosessinohjaus ja tarkastus. Jatkuvasti parantamalla leikkausteknologioita ja optimoimalla prosessimenetelmiä kiekkojen leikkauksen tarkkuutta ja vakautta voidaan parantaa entisestään, mikä tarjoaa luotettavampaa teknistä tukea puolijohdevalmistusteollisuudelle.
#03 Leikkauksen jälkeinen käsittely ja testaus
3.1 Puhdistus ja kuivaus
Kiekkojen leikkaamisen jälkeiset puhdistus- ja kuivausvaiheet ovat kriittisiä sirun laadun ja seuraavien prosessien sujuvan etenemisen varmistamiseksi. Tässä vaiheessa on tärkeää poistaa perusteellisesti piijäämät, jäähdytysnesteen jäämät ja muut leikkauksen aikana syntyvät epäpuhtaudet. Yhtä tärkeää on varmistaa, että sirut eivät vaurioidu puhdistusprosessin aikana, ja kuivauksen jälkeen varmistaa, ettei sirun pinnalle jää kosteutta, jotta vältetään esimerkiksi korroosio tai staattiset purkaukset.
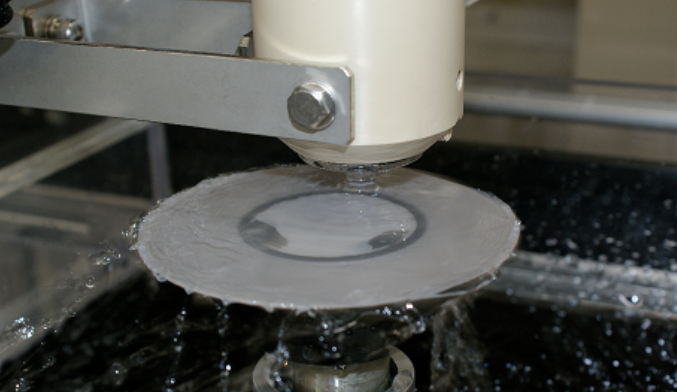
Leikkauksen jälkeinen käsittely: Puhdistus- ja kuivausprosessi
Prosessin vaihe | Sisältö | Vaikutus |
Puhdistusprosessi | -MenetelmäKäytä puhdistukseen erikoispuhdistusaineita ja puhdasta vettä yhdistettynä ultraääni- tai mekaaniseen harjaustekniikkaan. | Varmistaa epäpuhtauksien perusteellisen poiston ja estää lastujen vaurioitumisen puhdistuksen aikana. |
-Puhdistusaineen valintaValitse kiekkomateriaalin ja epäpuhtaustyypin perusteella varmistaaksesi tehokkaan puhdistuksen vahingoittamatta sirua. | Oikean puhdistusaineen valinta on avainasemassa tehokkaassa puhdistuksessa ja lohjen hylkimisessä. | |
-Parametrien hallinta: Tarkkaile puhdistuslämpötilaa, -aikaa ja -liuoksen pitoisuutta tarkasti estääksesi virheellisestä puhdistuksesta johtuvat laatuongelmat. | Kontrollit auttavat välttämään kiekon vaurioitumista tai epäpuhtauksien jäämistä jäljelle, mikä varmistaa tasaisen laadun. | |
Kuivausprosessi | -Perinteiset menetelmätLuonnollinen ilmakuivaus ja kuumailmakuivaus, joilla on alhainen hyötysuhde ja jotka voivat johtaa staattisen sähkön kertymiseen. | Voi johtaa hitaampaan kuivumisaikaan ja mahdollisiin staattisiin ongelmiin. |
-Nykyaikaiset teknologiatKäytä edistyneitä tekniikoita, kuten tyhjiökuivausta ja infrapunakuivausta, varmistaaksesi, että lastut kuivuvat nopeasti ja välttäen haitallisia vaikutuksia. | Nopeampi ja tehokkaampi kuivausprosessi, joka vähentää staattisen sähkön purkausten tai kosteusongelmien riskiä. | |
Laitteiden valinta ja huolto | -Laitteiden valintaTehokkaat puhdistus- ja kuivauskoneet parantavat prosessoinnin tehokkuutta ja hallitsevat tarkasti mahdollisia ongelmia käsittelyn aikana. | Korkealaatuiset koneet takaavat paremman käsittelyn ja vähentävät virheiden todennäköisyyttä puhdistuksen ja kuivauksen aikana. |
-Laitteiden huoltoLaitteiden säännöllinen tarkastus ja huolto varmistavat, että ne pysyvät optimaalisessa toimintakunnossa ja takaavat sirun laadun. | Asianmukainen huolto estää laitteiden toimintahäiriöt ja varmistaa luotettavan ja korkealaatuisen käsittelyn. |
Leikkauksen jälkeinen puhdistus ja kuivaus
Kiekkojen leikkaamisen jälkeiset puhdistus- ja kuivausvaiheet ovat monimutkaisia ja herkkiä prosesseja, jotka vaativat useiden tekijöiden huolellista huomioon ottamista lopullisen käsittelytuloksen varmistamiseksi. Tieteellisten menetelmien ja tiukkojen menettelyjen avulla on mahdollista varmistaa, että jokainen siru siirtyy seuraaviin pakkaus- ja testausvaiheisiin optimaalisessa kunnossa.
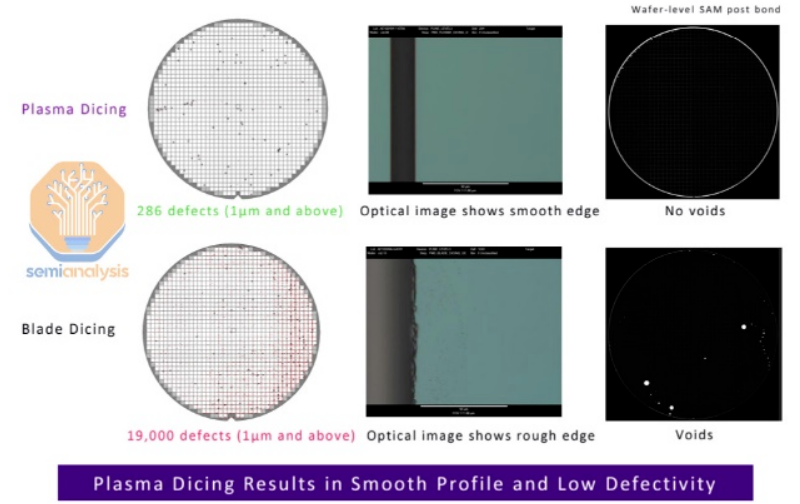
Leikkauksen jälkeinen tarkastus ja testaus
Vaihe | Sisältö | Vaikutus |
Tarkastusvaihe | 1.Visuaalinen tarkastusKäytä visuaalisia tai automaattisia tarkastuslaitteita tarkistaaksesi sirun pinnalla näkyviä vikoja, kuten halkeamia, lohkeamia tai epäpuhtauksia. Tunnista fyysisesti vaurioituneet sirut nopeasti jätteen välttämiseksi. | Auttaa tunnistamaan ja poistamaan vialliset lastut prosessin alkuvaiheessa, mikä vähentää materiaalihävikkiä. |
2.KokomittausKäytä tarkkuusmittauslaitteita lastun mittojen tarkkaan mittaamiseen, varmista, että leikkauskoko vastaa suunnitteluvaatimuksia ja estää suorituskykyongelmia tai pakkausvaikeuksia. | Varmistaa, että sirut ovat vaadittujen kokorajojen sisällä, estäen suorituskyvyn heikkenemisen tai kokoonpano-ongelmat. | |
3.Sähköinen suorituskykytestausArvioi keskeiset sähköiset parametrit, kuten resistanssi, kapasitanssi ja induktanssi, tunnistaaksesi vaatimustenvastaiset sirut ja varmistaaksesi, että vain suorituskykyyn pätevät sirut etenevät seuraavaan vaiheeseen. | Varmistaa, että prosessissa etenevät vain toiminnalliset ja suorituskykytestatut sirut, mikä vähentää vikaantumisriskiä myöhemmissä vaiheissa. | |
Testausvaihe | 1.Toiminnallinen testausVarmista, että sirun perustoiminnot toimivat tarkoitetulla tavalla, ja tunnista ja poista sirut, joissa on toiminnallisia poikkeavuuksia. | Varmistaa, että sirut täyttävät perustoiminnalliset vaatimukset ennen siirtymistä myöhempiin vaiheisiin. |
2.LuotettavuustestausArvioi sirun suorituskyvyn vakautta pitkäaikaisessa käytössä tai ankarissa ympäristöissä, tyypillisesti korkean lämpötilan vanhentamisen, matalan lämpötilan testauksen ja kosteustestauksen avulla todellisten äärimmäisten olosuhteiden simuloimiseksi. | Varmistaa, että sirut toimivat luotettavasti erilaisissa ympäristöolosuhteissa, mikä parantaa tuotteen pitkäikäisyyttä ja vakautta. | |
3.YhteensopivuustestausVarmista, että siru toimii oikein muiden komponenttien tai järjestelmien kanssa ja ettei yhteensopimattomuudesta johtuvia vikoja tai suorituskyvyn heikkenemistä esiinny. | Varmistaa sujuvan toiminnan reaalimaailman sovelluksissa estämällä yhteensopivuusongelmia. |
3.3 Pakkaus ja varastointi
Kiekkojen leikkaamisen jälkeen sirut ovat puolijohdevalmistusprosessin ratkaiseva tuotos, ja niiden pakkaus- ja varastointivaiheet ovat yhtä tärkeitä. Asianmukaiset pakkaus- ja varastointitoimenpiteet ovat olennaisia paitsi sirujen turvallisuuden ja vakauden varmistamiseksi kuljetuksen ja varastoinnin aikana, myös vahvan tuen tarjoamiseksi myöhemmille tuotanto-, testaus- ja pakkausvaiheille.
Tarkastus- ja testausvaiheiden yhteenveto:
Kiekkojen leikkaamisen jälkeiset sirujen tarkastus- ja testausvaiheet kattavat useita osa-alueita, mukaan lukien visuaalisen tarkastuksen, koon mittauksen, sähköisen suorituskyvyn testauksen, toiminnallisen testauksen, luotettavuustestauksen ja yhteensopivuustestauksen. Nämä vaiheet ovat yhteydessä toisiinsa ja täydentävät toisiaan muodostaen vankan esteen tuotteen laadun ja luotettavuuden varmistamiseksi. Tiukkojen tarkastus- ja testausmenettelyjen avulla mahdolliset ongelmat voidaan tunnistaa ja ratkaista nopeasti, mikä varmistaa, että lopputuote täyttää asiakkaan vaatimukset ja odotukset.
Aspect | Sisältö |
Pakkaustoimenpiteet | 1.AntistaattinenPakkausmateriaalien tulee olla erittäin antistaattisia, jotta staattinen sähkö ei vahingoita laitteita tai vaikuta niiden suorituskykyyn. |
2.KosteudenkestäväPakkausmateriaalien tulee olla hyvin kosteudenkestäviä, jotta estetään kosteuden aiheuttama korroosio ja sähköisten ominaisuuksien heikkeneminen. | |
3.IskunkestäväPakkausmateriaalien tulee vaimentaa tehokkaasti iskuja suojatakseen siruja tärinältä ja iskuilta kuljetuksen aikana. | |
Säilytysympäristö | 1.Kosteuden säätöPidä kosteus tarkasti asianmukaisella alueella estääksesi kosteuden imeytymisen ja korroosion, joka johtuu liiallisesta kosteudesta tai alhaisesta kosteudesta, aiheuttamista staattisista ongelmista. |
2.PuhtausPidä säilytysympäristö puhtaana, jotta lastut eivät saastu pölyllä ja epäpuhtauksilla. | |
3.Lämpötilan säätö: Aseta kohtuullinen lämpötila-alue ja pidä lämpötila vakaana estääksesi kiihtyneen ikääntymisen alhaisten lämpötilojen aiheuttamien liiallisen kuumuuden tai kondenssiongelmien vuoksi. | |
Säännöllinen tarkastus | Tarkasta ja arvioi varastoituja siruja säännöllisesti visuaalisten tarkastusten, kokomittausten ja sähköisten suorituskykytestien avulla mahdollisten ongelmien tunnistamiseksi ja korjaamiseksi ajoissa. Suunnittele sirujen käyttö varastointiajan ja -olosuhteiden perusteella varmistaaksesi, että niitä käytetään optimaalisessa kunnossa. |
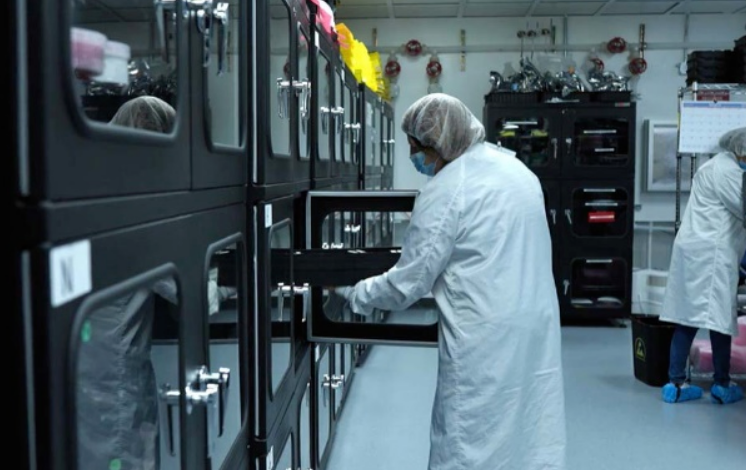
Mikrohalkeamien ja vaurioiden ongelma kiekkojen leikkausprosessin aikana on merkittävä haaste puolijohdevalmistuksessa. Leikkausjännitys on tämän ilmiön ensisijainen syy, sillä se aiheuttaa pieniä halkeamia ja vaurioita kiekon pinnalle, mikä johtaa valmistuskustannusten nousuun ja tuotteen laadun heikkenemiseen.
Tämän haasteen ratkaisemiseksi on ratkaisevan tärkeää minimoida leikkausjännitys ja ottaa käyttöön optimoidut leikkaustekniikat, työkalut ja olosuhteet. Huolellinen huomioiminen esimerkiksi terän materiaaliin, leikkausnopeuteen, paineeseen ja jäähdytysmenetelmiin voi auttaa vähentämään mikrohalkeamien muodostumista ja parantamaan prosessin kokonaistuottoa. Lisäksi meneillään oleva tutkimus kehittyneemmistä leikkausteknologioista, kuten laserleikkauksesta, etsii tapoja lieventää näitä ongelmia entisestään.
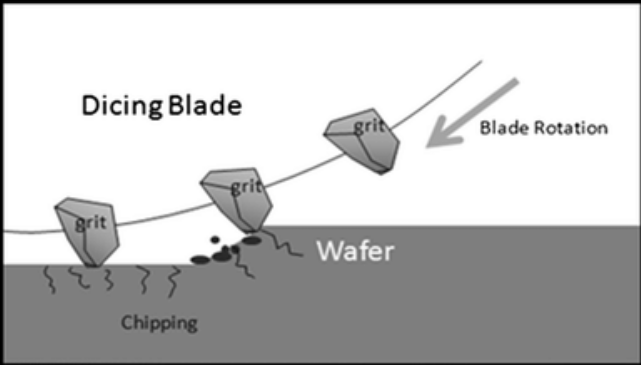
Hauraana materiaalina kiekot ovat alttiita sisäisille rakenteellisille muutoksille mekaanisen, lämpö- tai kemiallisen rasituksen vaikutuksesta, mikä johtaa mikrohalkeamien muodostumiseen. Vaikka nämä halkeamat eivät välttämättä ole heti havaittavissa, ne voivat laajentua ja aiheuttaa vakavampia vaurioita valmistusprosessin edetessä. Tämä ongelma tulee erityisen ongelmalliseksi myöhemmissä pakkaus- ja testausvaiheissa, joissa lämpötilanvaihtelut ja lisämekaaniset rasitukset voivat aiheuttaa näiden mikrohalkeamien kehittymisen näkyviksi murtumiksi, mikä voi johtaa sirun rikkoutumiseen.
Tämän riskin lieventämiseksi on tärkeää hallita leikkausprosessia huolellisesti optimoimalla parametreja, kuten leikkausnopeutta, painetta ja lämpötilaa. Vähemmän aggressiivisten leikkausmenetelmien, kuten laserleikkauksen, käyttö voi vähentää kiekkoon kohdistuvaa mekaanista rasitusta ja minimoida mikrohalkeamien muodostumisen. Lisäksi edistyneiden tarkastusmenetelmien, kuten infrapunaskannauksen tai röntgenkuvauksen, käyttöönotto kiekon paloitteluprosessin aikana voi auttaa havaitsemaan nämä varhaisvaiheen halkeamat ennen kuin ne aiheuttavat lisävaurioita.
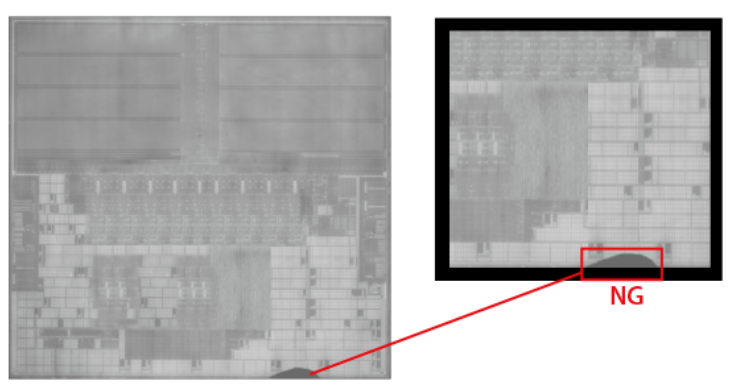
Kiekon pinnan vaurioituminen on merkittävä huolenaihe kuutiointiprosessissa, koska sillä voi olla suora vaikutus sirun suorituskykyyn ja luotettavuuteen. Tällaisia vaurioita voi aiheuttaa leikkaustyökalujen virheellinen käyttö, väärät leikkausparametrit tai itse kiekkoon liittyvät materiaalivirheet. Syystä riippumatta nämä vauriot voivat johtaa piirin sähköisen resistanssin tai kapasitanssin muutoksiin, mikä vaikuttaa kokonaissuorituskykyyn.
Näiden ongelmien ratkaisemiseksi tutkitaan kahta keskeistä strategiaa:
1. Leikkaustyökalujen ja parametrien optimointiKäyttämällä terävämpiä teriä, säätämällä leikkausnopeutta ja muokkaamalla leikkaussyvyyttä voidaan minimoida rasituksen keskittyminen leikkausprosessin aikana ja siten vähentää vaurioiden mahdollisuutta.
2. Uusien leikkaustekniikoiden tutkiminenEdistykselliset tekniikat, kuten laserleikkaus ja plasmaleikkaus, tarjoavat parempaa tarkkuutta ja samalla mahdollisesti vähentävät kiekolle aiheutuvia vaurioita. Näitä tekniikoita tutkitaan parhaillaan, jotta löydettäisiin tapoja saavuttaa korkea leikkaustarkkuus ja samalla minimoida kiekkoon kohdistuva lämpö- ja mekaaninen rasitus.
Lämpövaikutusalue ja sen vaikutukset suorituskykyyn
Lämpöleikkausprosesseissa, kuten laser- ja plasmaleikkauksessa, korkeat lämpötilat luovat väistämättä kiekon pinnalle lämpövaikutusalueen. Tämä alue, jossa lämpötilagradientti on merkittävä, voi muuttaa materiaalin ominaisuuksia ja siten vaikuttaa sirun lopulliseen suorituskykyyn.
Lämpövaikutusalueen (TAZ) vaikutus:
Kristallirakenteen muutoksetKorkeissa lämpötiloissa kiekkomateriaalin atomit voivat järjestyä uudelleen, mikä aiheuttaa vääristymiä kiderakenteessa. Tämä vääristymä heikentää materiaalia, vähentää sen mekaanista lujuutta ja vakautta, mikä lisää sirun rikkoutumisriskiä käytön aikana.
Sähköisten ominaisuuksien muutoksetKorkeat lämpötilat voivat muuttaa puolijohdemateriaalien varauksenkuljettajien pitoisuutta ja liikkuvuutta, mikä vaikuttaa sirun sähkönjohtavuuteen ja virransiirtotehokkuuteen. Nämä muutokset voivat johtaa sirun suorituskyvyn heikkenemiseen, mikä voi tehdä siitä sopimattoman aiottuun tarkoitukseen.
Näiden vaikutusten lieventämiseksi lämpötilan hallinta leikkauksen aikana, leikkausparametrien optimointi ja menetelmien, kuten jäähdytyssuihkujen tai jälkikäsittelyjen, tutkiminen ovat olennaisia strategioita lämpövaikutuksen laajuuden vähentämiseksi ja materiaalin eheyden säilyttämiseksi.
Kaiken kaikkiaan sekä mikrohalkeamat että lämpövaikutusvyöhykkeet ovat ratkaisevia haasteita kiekkojen kuutiointitekniikassa. Jatkuva tutkimus sekä teknologinen kehitys ja laadunvalvontatoimenpiteet ovat välttämättömiä puolijohdetuotteiden laadun parantamiseksi ja niiden markkinakilpailukyvyn lisäämiseksi.
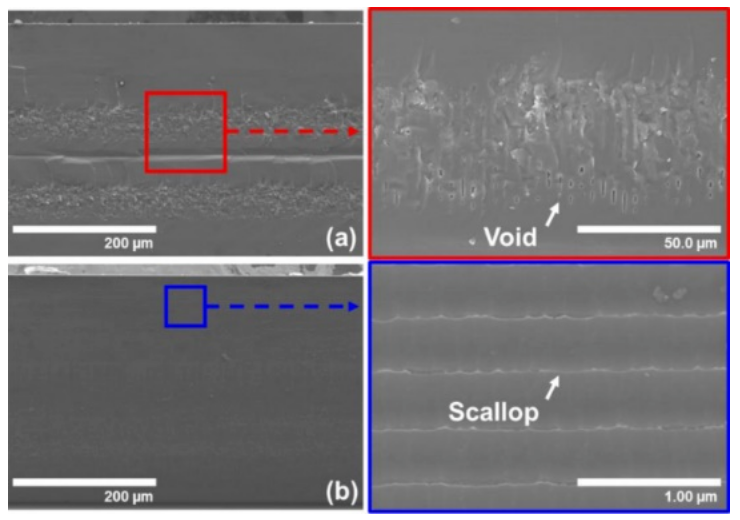
Toimenpiteet lämpövaikutusalueen hallitsemiseksi:
Leikkausprosessiparametrien optimointiLeikkausnopeuden ja -tehon pienentäminen voi tehokkaasti minimoida lämpövaikutusalueen (TAZ) koon. Tämä auttaa hallitsemaan leikkausprosessin aikana syntyvän lämmön määrää, mikä vaikuttaa suoraan kiekon materiaaliominaisuuksiin.
Edistykselliset jäähdytystekniikatNestemäisen typen jäähdytyksen ja mikrofluidijäähdytyksen kaltaisten tekniikoiden käyttö voi merkittävästi rajoittaa lämpövaikutusalueen aluetta. Nämä jäähdytysmenetelmät auttavat haihduttamaan lämpöä tehokkaammin, mikä säilyttää kiekon materiaaliominaisuudet ja minimoi lämpövauriot.
MateriaalivalintaTutkijat tutkivat uusia materiaaleja, kuten hiilinanoputkia ja grafeenia, joilla on erinomainen lämmönjohtavuus ja mekaaninen lujuus. Nämä materiaalit voivat pienentää lämpövaikutusaluetta ja samalla parantaa sirujen yleistä suorituskykyä.
Yhteenvetona voidaan todeta, että vaikka terminen iskualue on väistämätön seuraus lämpöleikkaustekniikoista, sitä voidaan tehokkaasti hallita optimoiduilla prosessointitekniikoilla ja materiaalivalinnoilla. Tuleva tutkimus keskittyy todennäköisesti lämpöleikkausprosessien hienosäätöön ja automatisointiin tehokkaamman ja tarkemman kiekkojen paloittelun saavuttamiseksi.

Tasapainostrategia:
Kiekkojen tuoton ja tuotantotehokkuuden välisen optimaalisen tasapainon saavuttaminen on jatkuva haaste kiekkojen kuutiointiteknologiassa. Valmistajien on otettava huomioon useita tekijöitä, kuten markkinoiden kysyntä, tuotantokustannukset ja tuotteen laatu, kehittääkseen järkevän tuotantostrategian ja prosessiparametrit. Samalla edistyneiden leikkauslaitteiden käyttöönotto, käyttäjien taitojen parantaminen ja raaka-aineiden laadunvalvonnan tehostaminen ovat olennaisia tuoton ylläpitämiseksi tai jopa parantamiseksi samalla, kun tuotantotehokkuutta lisätään.
Tulevaisuuden haasteet ja mahdollisuudet:
Puolijohdeteknologian kehittyessä kiekkojen leikkaus kohtaa uusia haasteita ja mahdollisuuksia. Sirujen koon pienentyessä ja integraation lisääntyessä leikkaustarkkuuden ja -laadun vaatimukset kasvavat merkittävästi. Samanaikaisesti kehittyvät teknologiat tarjoavat uusia ideoita kiekkojen leikkaustekniikoiden kehittämiseen. Valmistajien on pysyttävä ajan tasalla markkinoiden dynamiikasta ja teknologisista trendeistä sekä jatkuvasti mukautettava ja optimoitava tuotantostrategioita ja prosessiparametreja vastatakseen markkinoiden muutoksiin ja teknologisiin vaatimuksiin.
Yhteenvetona voidaan todeta, että yhdistämällä markkinoiden kysynnän, tuotantokustannusten ja tuotteen laadun näkökohdat sekä ottamalla käyttöön edistyneitä laitteita ja teknologiaa, parantamalla käyttäjien taitoja ja vahvistamalla raaka-aineiden hallintaa valmistajat voivat saavuttaa parhaan tasapainon kiekkojen saannon ja tuotantotehokkuuden välillä kiekkojen paloittelun aikana, mikä johtaa tehokkaaseen ja korkealaatuiseen puolijohdetuotteiden tuotantoon.
Tulevaisuudennäkymät:
Nopean teknologisen kehityksen myötä puolijohdeteknologia kehittyy ennennäkemättömän nopeasti. Kriittisenä askeleena puolijohdevalmistuksessa kiekkojen leikkausteknologia on valmiina jännittäviin uusiin kehitysaskeliin. Tulevaisuudessa kiekkojen leikkausteknologian odotetaan saavuttavan merkittäviä parannuksia tarkkuuteen, tehokkuuteen ja kustannuksiin, mikä tuo uutta elinvoimaa puolijohdeteollisuuden jatkuvaan kasvuun.
Tarkkuuden lisääminen:
Tarkkuuden tavoittelussa kiekkojen leikkausteknologia tulee jatkuvasti venyttämään nykyisten prosessien rajoja. Tutkimalla perusteellisesti leikkausprosessin fysikaalisia ja kemiallisia mekanismeja ja hallitsemalla leikkausparametreja tarkasti saavutetaan hienompia leikkaustuloksia, jotka täyttävät yhä monimutkaisemmat piirisuunnitteluvaatimukset. Lisäksi uusien materiaalien ja leikkausmenetelmien tutkiminen parantaa merkittävästi saantoa ja laatua.
Tehokkuuden parantaminen:
Uudet kiekkojen leikkauslaitteet keskittyvät älykkääseen ja automatisoituun suunnitteluun. Edistyneiden ohjausjärjestelmien ja algoritmien käyttöönotto mahdollistaa laitteiden automaattisen leikkausparametrien säätämisen erilaisten materiaalien ja suunnitteluvaatimusten mukaan, mikä parantaa merkittävästi tuotannon tehokkuutta. Innovaatiot, kuten monikiekkojen leikkaustekniikka ja nopeat teränvaihtojärjestelmät, ovat ratkaisevassa roolissa tehokkuuden parantamisessa.
Kustannusten vähentäminen:
Kustannusten alentaminen on kiekkojen leikkausteknologian kehityksen keskeinen suunta. Uusien materiaalien ja leikkausmenetelmien kehittyessä laitteiden kustannusten ja ylläpitokulujen odotetaan olevan tehokkaasti hallinnassa. Lisäksi tuotantoprosessien optimointi ja hylkytuotteiden määrän vähentäminen vähentävät entisestään valmistuksen aikaista jätettä, mikä johtaa kokonaistuotantokustannusten alenemiseen.
Älykäs valmistus ja esineiden internet:
Älykkään valmistuksen ja esineiden internetin (IoT) teknologioiden integrointi tuo mullistavia muutoksia kiekkojen leikkausteknologiaan. Laitteiden välisen yhteenliitettävyyden ja tiedon jakamisen avulla tuotantoprosessin jokaista vaihetta voidaan seurata ja optimoida reaaliajassa. Tämä ei ainoastaan paranna tuotannon tehokkuutta ja tuotteiden laatua, vaan tarjoaa yrityksille myös tarkempaa markkinaennustetta ja päätöksenteon tukea.
Tulevaisuudessa kiekkojen leikkausteknologia tulee tekemään merkittäviä edistysaskeleita tarkkuuden, tehokkuuden ja kustannusten suhteen. Nämä edistysaskeleet vauhdittavat puolijohdeteollisuuden jatkuvaa kehitystä ja tuovat lisää teknologisia innovaatioita ja mukavuuksia ihmisyhteiskuntaan.
Julkaisun aika: 19.11.2024